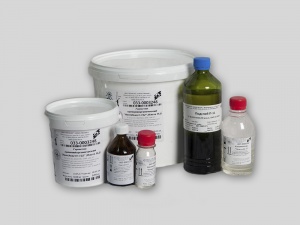
Пентэласт-722
ТУ 2513-011-40245042-99
Аналог "Виксинт У–4-21" ТУ 38.303-04-04-90
ОБЛАСТЬ ПРИМЕНЕНИЯ
Герметик "ПЕНТЭЛАСТ-722" при температуре прогрева до +100 °С может применять¬ся в контакте с серебряными и оловянными покрытиями, медью и хромовой бронзой. Применяется для об¬волакивания плат, крепления радио-элементов и в качестве теплоизоляционного материала.
СОСТАВ И СВОЙСТВА
Герметик "ПЕНТЭЛАСТ-722" является двухкомпонентным и поставляется в виде – пасты "П-3" и катализатора № 21 (ТУ 38.303.-04-05-90). По внешнему виду паста "П-3" представляет собой вязкотекучий материал белого цвета, без механических включений. Допускается незначительное количество агломерированных частиц наполнителя, исчезающих при перемешивании. Паста "П-3" должна храниться в складских условиях при температуре от 0 до 30 °С.
Герметик "ПЕНТЭЛАСТ-722" по степени воздействия на организм человека, относится к 4 классу опасности по ГОСТ 12.1.007-76 (вещества малоопасные). Он трудногорюч, не обладает раздражающим действием на кожу и слизистые оболочки человека и не образует токсичных соединений в воздушной среде и сточных водах в присутствии других веществ или факторов.
В вулканизованном состоянии герметик "ПЕНТЭЛАСТ-722" представляет собой прочную, эластичную непрозрачную резиноподобную массу белого цвета. По своим характеристикам он должен соответствовать требованиям и нормам, указанным в таблице:
№ | Наименование показателя | Норма по ТУ | Типичное значение |
---|---|---|---|
1. | Жизнеспособность в ч., в пределах | 0,5 – 6,0 | 1,5 - 2,0 |
2. | Условная прочность при разры¬ве, МПа, не менее | 1,5 | 2,2 –2,4 |
3. | Относительное уд¬линение при раз¬рыве, %, не менее | 110 | 198 - 210 |
4. | Электрическая прочность, кВ/мм | 13,0 | 13,0 |
5. | Прочность связи (адгезия) герметика с металлом по подслою при отслаивании от алюминиевого сплава Д16 (разрыв по матери¬алу или отслаивание по сетке), кН/м, не менее | 0,5 | 0,5 |
6. | Твердость по Шору А, усл. Ед. в пределах | 42 - 55 | 45 - 55 |
Технология работы
Герметик получают смешиванием пасты "П-3" и катализатора в следующих соотношениях: паста "П-3" - 100 м.ч., катализатор № 21 – 2,5 м.ч., режим вулканизации 72 часа при 20°С. Для получения большей адгезии к поверхности можно применять подслой П-11 или П-12Э (ТУ 38. 303-04-06-90).
СПОСОБ ПРИМЕНЕНИЯ
Поверхность образца должна быть чистой и свободной от загрязнений. Поверхность изделий, подлежащих герметизации, обрабатывают одним из указанных способов:
А) в случае незащищенного металла поверхность обрабатывают любым механическим способом до металлического блеска;
Б) неметаллические поверхности зашкуривают до удаления глянца;
В) металлические поверхности с антикоррозионными защитными гальваническими покрытиями (анодированные, хромированные и др.) очищают от стружки и пыли волосяными щетками и пылесосом.
Подготовленные поверхности обезжиривают. При обезжиривании поверхность протирают чистыми салфетками, смоченными бензином, сушат на воздухе 10-15 мин., затем протирают салфетками, смоченными ацетоном, и вновь сушат на воздухе 10-15 мин.
Ширина обезжириваемой поверхности должна на 30-40 мм превышать ширину поверхности, покрываемой подслоем.
Ширина поверхности, покрываемой подслоем должна быть на 15-20 мм больше ширины герметизируемой поверхности.
Во избежание загрязнения герметизируемой поверхности деталей подслой следует обезжиривать непосредственно перед нанесением подслоя.
Интервал времени между обезжириванием и нанесением подслоя не должен превышать 3-4 часов. При превышении этого срока следует провести повторное обезжиривание.
На подготовленные таким образом поверхности чистой кисточкой наносят один раз равномерным слоем подслой П-11 или П12Э. Сушат на воздухе при температуре 15-30 °С 40 - 60 минут. Герметик должен быть нанесён на поверхность изделия не позднее, чем через сутки после нанесения подслоя. При загрязнении или выдержке поверхности с нанесённым подслоем более одних суток ранее нанесённый подслой тщательно смывают бензином и вновь обрабатывают подслоем.
Смешение
Тщательно перемешайте основу перед употреблением, из-за возможного разделения с наполнителем при длительном хранении.
Cмешать до полного распределения отвердителя в основе. Смешивайте достаточно малые количества, чтобы добиться тщательного перемешивания основы и отвердителя. Плохо промешанная масса отвердится неполностью. Смешение можно производить вручную или механически, но не перемешивайте слишком долго, т. к. при долгом перемешивании образуется много пузырьков воздуха. Также не рекомендуется повышать температуру выше 25°С, т. к. при повышенной температуре и влажности воздуха время жизни компаунда сокращается.
Для удаления воздушных пузырей рекомендуется использовать вакуумную камеру, при этом смесь будет увеличиваться в объеме в 2-3 раза, а затем оседать. Поэтому необходимо использовать достаточно большую емкость.
После 1-2 минутного вакуумирования смесь должна быть проверена и, при отсутствии воздушных пузырей, может использоваться далее.
Осторожно! Продолжительное вакуумирование приведет к удалению летучих компонентов из смеси и может вызвать плохое отверждение утолщенных частей и появление нехарактерных свойств.
Примечание - Если нет подходящего оборудования для вакуумирования, то воздушные включения могут быть минимизированы путем смешения небольших количеств основы и отвердителя. Используя кисть, нанесите на образец тонкий слой компаунда и оставьте при комнатной температуре до тех пор, пока поверхность не очистится от пузырьков и не начнет отверждаться. После этого смешивайте следующие порции основы и отвердителя и повторяйте все до получения готового слепка.
Заливка смеси и отверждение
Как можно быстрее вылейте смесь основы с отвердителем на исходный образец, который был предварительно обработан подслоем, стараясь избежать попадания воздушных пузырьков. Материал будет отверждаться до состояния эластичной резины в течении 24 часов. Если рабочая температура значительно ниже чем 23 °С, то время отверждения увеличивается. Конечные механические свойства будут достигнуты через 72 часа.